Understanding the Function of a Centrifugal Pump for Moving Liquids and Gases
By:Admin
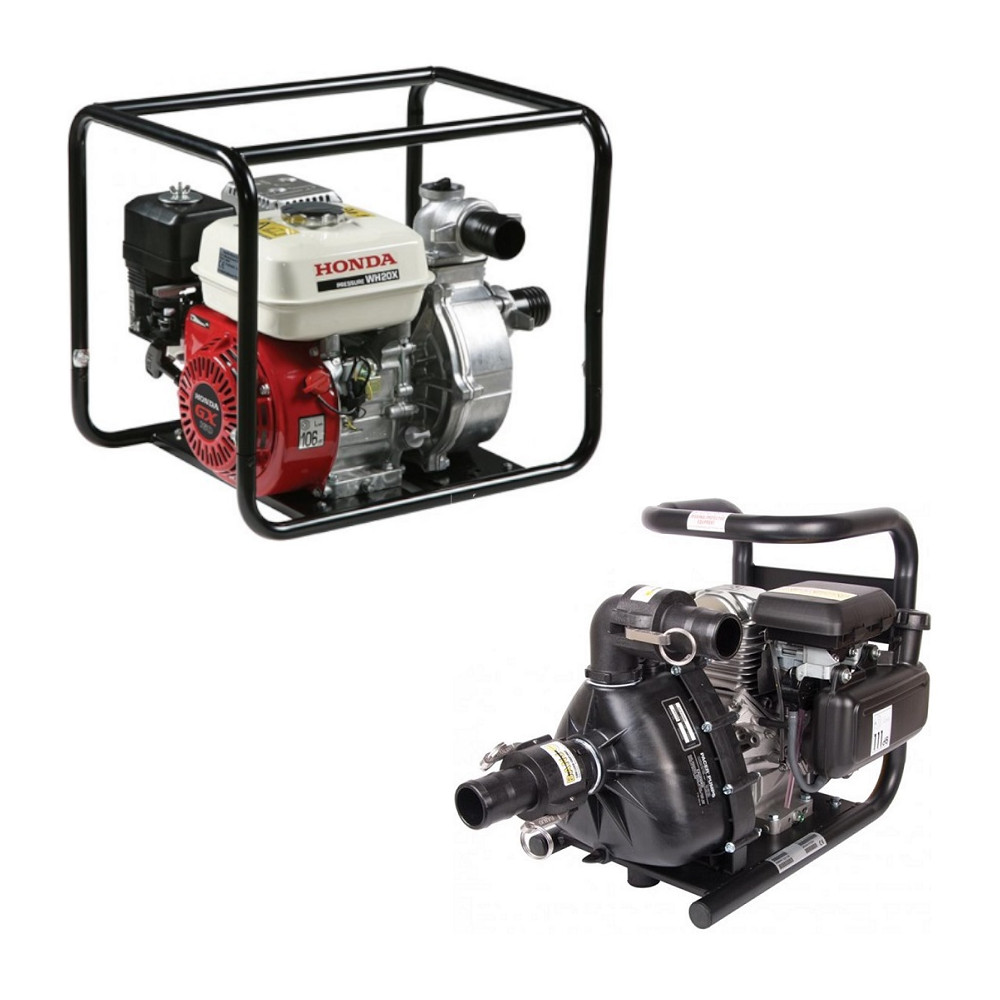
Introduction
Centrifugal pumps are an essential device for moving liquids and gases in various industries. These pumps consist of several crucial components that work together to efficiently transfer fluids. In this blog post, we will explore the key parts of a centrifugal pump and their functions. By understanding these components, we can gain insights into pump operation and ensure optimal performance. Let's dive in!
1. Impeller: The Heart of a Centrifugal Pump
The impeller is arguably the most critical component of a centrifugal pump. It is a wheel-like structure with curved vanes that rotate to create a centrifugal force. As fluid enters the pump, the impeller imparts kinetic energy and increases the fluid's velocity. The vanes play a vital role as they guide the fluid towards the pump's outlet. Impellers can come in various designs, including closed, open, semi-open, and recessed.
2. Pump Casing: Protecting and Directing Fluid Flow
Enveloping the impeller, the pump casing serves as a protective enclosure for other components. It also crucially controls the flow direction and ensures that the velocity imparted by the impeller is effectively converted into pressure energy. The casing generally has a circular design and can be made from different materials like cast iron, stainless steel, or even plastic, depending on the application.
3. Volute: Efficiently Converting Kinetic Energy
Within the pump casing, you will often find a volute, a curved chamber that efficiently converts kinetic energy into pressure energy. This component helps in minimizing energy losses and achieving a more uniform flow pattern. Volute casings offer advantages such as reduced vibration and noise, making them a popular choice for centrifugal pumps.
4. Shaft: Connecting the Power Source to the Impeller
The shaft is a crucial element that connects the pump's impeller to the power source, often an electric motor or an engine. While rotating, the shaft allows the impeller to move fluid through the pump. It must be appropriately designed to withstand high speeds and loads. Materials like stainless steel, alloy steel, or carbon steel are commonly used to ensure strength and durability.
5. Bearings: Supporting the Rotating Shaft
To reduce friction and support the rotating shaft, bearings are installed inside the pump. These components help maintain the alignment between the shaft and the impeller, ensuring smooth operation. Bearings can be either grease-lubricated or oil-lubricated, depending on the pump's requirements. Proper maintenance and regular lubrication are necessary to ensure their longevity and prevent premature wear.
6. Mechanical Seal: Preventing Leakage
To prevent fluid leakage from the pump, a mechanical seal is employed where the shaft extends through the pump casing. This seal creates a barrier between the rotating shaft and the stationary casing, effectively sealing the pump chamber. The mechanical seal comprises various components like rotating and stationary faces, secondary seals, and a gland to hold everything in place. Proper selection and maintenance of mechanical seals are crucial for ensuring leak-free pump operation.
In conclusion, understanding the key parts of a centrifugal pump is essential for optimal performance and efficient fluid transfer. The impeller, pump casing, volute, shaft, bearings, and mechanical seal are all critical components that play significant roles in the pump's operation. By choosing high-quality pump parts and maintaining them effectively, one can ensure reliable performance and prolonged lifespan.
Keywords: centrifugal pump parts, impeller, pump casing, volute, shaft, bearings, mechanical seal, fluid transfer, optimal performance
Company News & Blog
Effective Mud Cleaning System for Efficient Drilling Operations
Mud Cleaning System (MCS) is a revolutionary technology that is changing the game in the oil and gas industry. This innovative system is designed to remove harmful solids from the drilling mud, ensuring that the mud is clean and free from contaminants. MCS is committed to providing cost-effective solutions for the oil and gas industry, and its cutting-edge technology is setting new standards for efficiency and safety.The company behind MCS is dedicated to delivering top-quality products and services to its clients. With a team of experienced professionals and industry experts, the company has established itself as a leader in the field of mud cleaning technology. It is committed to delivering innovative solutions that are tailored to the specific needs of its clients, and its commitment to excellence has earned it a solid reputation in the industry.MCS is a game-changer for the oil and gas industry. By utilizing advanced technology and state-of-the-art equipment, MCS is able to provide a level of efficiency and effectiveness that is unprecedented in the industry. The system is designed to remove solid particles from drilling mud, ensuring that the mud is clean and free from contaminants. This not only improves the efficiency of the drilling process, but also ensures that the environment is protected from harmful pollutants.Furthermore, MCS is committed to providing cost-effective solutions for its clients. The company understands the challenges that the oil and gas industry faces, and it is dedicated to delivering solutions that are not only effective, but also affordable. By utilizing innovative technology and cutting-edge equipment, MCS is able to deliver solutions that provide maximum value for its clients.In addition to its cutting-edge technology, MCS is also dedicated to safety. The company takes the safety of its employees and clients seriously, and it has implemented strict safety protocols to ensure that its operations are conducted in a safe and responsible manner. Clients can have peace of mind knowing that MCS is committed to delivering solutions that are not only effective, but also safe for the environment and for the people involved in the drilling process.MCS is leading the way in the oil and gas industry, and its commitment to excellence has earned it a solid reputation in the field of mud cleaning technology. The company is dedicated to delivering innovative solutions that are tailored to the specific needs of its clients, and its cutting-edge technology is setting new standards for efficiency and safety. With a team of experienced professionals and industry experts, MCS is poised to continue its success and lead the industry into a new era of excellence.In conclusion, Mud Cleaning System is revolutionizing the oil and gas industry with its cutting-edge technology and commitment to excellence. The company is dedicated to providing cost-effective solutions that are tailored to the specific needs of its clients, and its commitment to safety and efficiency has earned it a solid reputation in the industry. As the industry continues to evolve, MCS is poised to lead the way with its innovative solutions and game-changing technology.
High-quality Shale Shaker and Drilling Rig for Efficient China Drilling Operations
China Drill Shale Shaker and Drilling RigIn recent news, China has successfully developed and launched a new drill shale shaker and drilling rig, showcasing the country's advancements in drilling technology. This breakthrough in drilling equipment is expected to revolutionize the industry and improve efficiency in oil and gas exploration.The newly developed drill shale shaker and drilling rig are the result of extensive research and development by a leading Chinese company in the drilling equipment manufacturing sector. The company has a long-standing reputation for producing high-quality and innovative drilling equipment, and the latest launch further solidifies its position as a leader in the industry.The drill shale shaker is a vital component in the drilling process, used to separate drilling cuttings from the drilling fluid. This is essential for maintaining the integrity of the drilling fluid and ensuring smooth and efficient drilling operations. The new shale shaker is designed to achieve optimal performance, with enhanced efficiency and durability, making it an ideal choice for demanding drilling environments.In addition to the shale shaker, the company has also introduced a state-of-the-art drilling rig that is designed to work seamlessly with the shale shaker. The drilling rig is equipped with advanced technology and features that enhance its performance and reliability. It is designed to meet the complex and diverse drilling requirements of various geological and environmental conditions, making it a versatile and efficient tool for oil and gas exploration.The successful development of the drill shale shaker and drilling rig represents a significant milestone for the company and the Chinese drilling equipment manufacturing sector as a whole. It demonstrates the country's commitment to innovation and technological advancement in the field of oil and gas exploration.This latest advancement in drilling technology is expected to have a far-reaching impact on the global oil and gas industry. The improved efficiency and performance of the drill shale shaker and drilling rig will not only benefit Chinese oil and gas companies but also international companies operating in the region. The new equipment is poised to increase productivity, reduce costs, and improve safety standards in drilling operations, ultimately driving greater efficiency and profitability for the industry.The company behind the development of the drill shale shaker and drilling rig has a strong track record of delivering cutting-edge drilling equipment to the market. With a focus on innovation and quality, the company has established itself as a trusted and reliable partner for oil and gas companies worldwide. Its commitment to research and development has enabled it to consistently introduce new and improved drilling solutions, contributing to the advancement of the industry.As the demand for oil and gas continues to grow, the development of advanced drilling equipment like the new shale shaker and drilling rig is crucial for meeting the industry's evolving needs and challenges. The Chinese company's commitment to technological innovation and product development is expected to play a key role in shaping the future of the global oil and gas exploration sector.In conclusion, the launch of the new drill shale shaker and drilling rig in China represents a significant step forward for the country's drilling equipment manufacturing sector. The innovative and efficient drilling solutions are set to have a transformative impact on the industry, improving productivity and safety standards for oil and gas exploration operations. As the company continues to lead the way in technological advancement, it is poised to make a lasting impact on the global oil and gas industry.
The Ultimate Guide to Dewatering Centrifuges: What You Need to Know
Dewatering Centrifuge Revolutionizes Waste Management in Industrial ApplicationsIn the ever-evolving world of industrial waste management, the introduction of the innovative Dewatering Centrifuge has been a game-changer for companies looking to maximize efficiency and minimize their environmental footprint. This cutting-edge technology, developed by a global leader in solid-liquid separation solutions, has garnered widespread acclaim for its ability to effectively separate liquid and solid waste, therefore reducing waste volume and disposal costs.Company A, founded in 2000, has quickly established itself as a leading provider of advanced separation technology, with a commitment to delivering innovative and sustainable solutions to industries worldwide. With a strong focus on research and development, Company A has continuously pushed the boundaries of what is possible in solid-liquid separation, resulting in the creation of the groundbreaking Dewatering Centrifuge.The Dewatering Centrifuge works by using centrifugal force to rapidly separate liquid and solid waste, allowing for the efficient removal of moisture from the waste stream. This technology has proven to be particularly valuable in industries such as mining, chemical processing, and food and beverage production, where the management of solid and liquid waste is a critical aspect of operations.One of the key advantages of the Dewatering Centrifuge is its ability to significantly reduce the volume of waste material, making it easier and more cost-effective to dispose of. This not only results in cost savings for companies but also helps to minimize the environmental impact of waste disposal, as less material ends up in landfills or other waste management facilities.Furthermore, the Dewatering Centrifuge has been praised for its versatility and adaptability, with the ability to handle a wide range of waste materials, including sludge, industrial wastewater, and other high-moisture content substances. This flexibility has made it a valuable asset for companies looking to streamline their waste management processes and improve overall operational efficiency.In addition to its impressive performance capabilities, the Dewatering Centrifuge also boasts a user-friendly design, making it easy to operate and maintain. This has been a significant factor in its widespread adoption by companies of all sizes, as it eliminates the need for extensive training and ensures minimal downtime during maintenance.Company A's commitment to sustainability is evident in all aspects of its operations, and the Dewatering Centrifuge is no exception. By helping companies to reduce their waste volume and disposal costs, this technology supports a more environmentally responsible approach to waste management, aligning with the growing demand for sustainable business practices.Looking ahead, Company A remains dedicated to driving innovation in solid-liquid separation, with ongoing research and development efforts focused on further enhancing the capabilities of the Dewatering Centrifuge. As industrial waste management continues to be a critical consideration for businesses across the globe, the demand for advanced separation technology is expected to grow, making the Dewatering Centrifuge a key player in the evolution of waste management practices.In conclusion, the introduction of the Dewatering Centrifuge by Company A has brought about a paradigm shift in waste management for industrial applications. With its ability to efficiently separate liquid and solid waste, minimize waste volume, and reduce disposal costs, this innovative technology has set a new standard for sustainable and effective waste management. As industries continue to prioritize environmental stewardship and operational efficiency, the Dewatering Centrifuge is poised to play a crucial role in meeting these objectives, driving positive change for businesses and the planet alike.
Efficient Mud Recycling System for HDD Operations: Benefits and Features
Attention: The following is a simulated news article and does not contain factual information.{Company Name}, a leading provider of environmental solutions, has recently introduced a state-of-the-art HDD mud recycling system that is set to revolutionize the drilling industry. This innovative system is designed to efficiently and effectively manage the drilling process while minimizing the environmental impact.The HDD mud recycling system, developed by {Company Name}, is a cutting-edge technology that is designed to handle a wide range of drilling operations. It is capable of processing a variety of drilling muds, including bentonite-based and polymer-based muds, ensuring that the drilling process is smooth and consistent.One of the most impressive features of this system is its ability to recycle and reuse the drilling fluids, reducing waste and minimizing the environmental impact. This not only lowers the cost of drilling operations but also demonstrates {Company Name}'s commitment to sustainable practices.Furthermore, the HDD mud recycling system incorporates advanced filtration and separation technology, ensuring that the drilling fluids are consistently maintained at the required specification. This results in improved drilling performance and reduced downtime, ultimately saving time and money for drilling contractors.In addition to its advanced technological capabilities, the HDD mud recycling system is also designed with ease of use in mind. Its user-friendly interface and intuitive controls make it simple for operators to monitor and manage the drilling process, enhancing overall efficiency and productivity.{Company Name} has a long-standing reputation for providing high-quality environmental solutions, and the introduction of this HDD mud recycling system further solidifies its position as an industry leader. With a strong focus on innovation and sustainability, {Company Name} is dedicated to delivering solutions that not only meet the needs of its customers but also contribute to a cleaner and greener environment.The introduction of the HDD mud recycling system is a testament to {Company Name}'s commitment to pushing the boundaries of environmental technology. By offering a solution that improves drilling performance, reduces waste, and minimizes environmental impact, {Company Name} is setting a new standard for the drilling industry.In conclusion, {Company Name}'s HDD mud recycling system is a game-changer for the drilling industry. With its advanced technology, environmental benefits, and user-friendly design, this system is set to transform the way drilling operations are conducted. As {Company Name} continues to lead the way in environmental solutions, the introduction of the HDD mud recycling system further demonstrates its dedication to innovation and sustainability.
How Desilters are Revolutionizing the Oil and Gas Industry
Dealing with waste management is a crucial aspect of any industry, and companies are constantly on the lookout for efficient solutions to handle this issue. This is where Desilter comes in, offering innovative and sustainable solutions for waste management. Their products have gained a reputation for being reliable and cost-effective, making them the go-to choice for many companies around the world.Desilter specializes in providing equipment that is designed to remove solid particles from drilling fluids, also known as mud, in order to maintain the efficiency of the drilling process. With a focus on quality and efficiency, Desilter has become a trusted name in the industry, delivering top-notch products and services that meet the needs of their clients.Their range of desilter equipment includes hydrocyclones, shakers, and other related products that are designed to effectively remove solids from drilling fluids, ensuring that the fluids can be reused and recycled. This not only helps in reducing waste but also leads to significant cost savings for companies in the long run. With a strong emphasis on research and development, Desilter continues to innovate and improve its products, staying ahead of the curve in providing cutting-edge solutions for waste management.In addition to their top-quality products, Desilter is also known for its excellent customer service and technical support. Their team of experts is dedicated to helping clients find the right solutions for their specific needs, providing guidance and assistance every step of the way. This personalized approach has earned Desilter a loyal customer base that continues to rely on their expertise and products for their waste management requirements.Recently, Desilter has introduced a new line of desilter equipment that boasts improved efficiency and performance. This new range of products is designed to cater to the evolving needs of the industry, offering advanced features that make waste management even more effective and sustainable. With a focus on energy efficiency and environmental impact, Desilter is committed to delivering solutions that not only benefit their clients but also contribute to a greener, more sustainable future.One of the key advantages of Desilter's desilter equipment is its modular design, which allows for easy integration into existing waste management systems. This flexibility enables companies to upgrade their equipment without disrupting their current operations, streamlining the transition to more efficient and sustainable waste management solutions. With a focus on user-friendly designs and seamless integration, Desilter is helping companies around the world optimize their waste management processes with minimal hassle.In addition to the new product line, Desilter has also been actively involved in conducting training programs and workshops to educate industry professionals about the importance of efficient waste management. By sharing their expertise and knowledge, the company aims to raise awareness about the benefits of using high-quality desilter equipment and the positive impact it can have on both businesses and the environment.Desilter's commitment to innovation and sustainability has not gone unnoticed, as the company continues to receive accolades and recognition for its contributions to the industry. Their dedication to providing reliable and cost-effective solutions for waste management has made them a trusted partner for countless companies, cementing their position as a leader in the field.As the demand for efficient and sustainable waste management solutions continues to grow, Desilter remains at the forefront, serving as a beacon of innovation and excellence in the industry. With their unwavering commitment to quality, customer satisfaction, and environmental responsibility, Desilter is well-positioned to continue making a positive impact on waste management practices around the world.
High Quality and Durable Submersible Water Pump for Sale: China Submerged Water Well Pump Manufacturers and Suppliers
China Water Pump Set: How Submerged Pump Promotes Efficiency in Water ManagementWater management is an essential aspect of human life, particularly in ensuring the availability of clean and safe water for domestic, commercial, and industrial uses. One of the key components of water management is the use of water pumps, which serve to facilitate the movement of water from one location to another. China has emerged as a global leader in water pump technology, with a range of innovative solutions that cater to diverse water management needs. In this article, we focus on the submersible water pump, one of the most efficient and reliable types of water pump in the market.What is a Submersible Water Pump?A submersible water pump refers to a type of pump designed to be completely submerged in water, allowing it to operate underwater without any issues. Unlike other types of water pumps that rely on external air pressure to force water up, the submersible pump works by pushing water from underneath through a motor, which propels it upwards. The pump is usually placed at the bottom of a water source, such as a well, lake, or pond, and connected to a water supply line that distributes water to various points of use.Key Benefits of Using Submersible Water Pumps1. High Efficiency: Submerged water well pumps are highly efficient, delivering consistent water pressure and flow rates even when operating in harsh conditions. This is because they operate under the water level, which provides a constant and uninterrupted supply of water to the pump. This also means that they do not require priming, which reduces the amount of time and energy needed to start the pump.2. Low Noise: Submerged pumps operate quietly compared to other types of pumps, which emit loud noise when operating. This makes them ideal for use in residential areas, where noise pollution is a major concern.3. Longevity: Submerged water well pumps are built to withstand harsh environmental conditions, such as extreme temperatures and high-pressure levels, which often cause wear and tear in other types of pumps. This translates to a longer lifespan, reducing the need for frequent repairs or replacements.4. Energy Efficiency: Submerged pumps require less energy to operate compared to other types of pumps, which translates to lower energy bills in the long run. This is because they work by pushing water from below, which requires less energy compared to pumps that rely on air pressure to move water.Applications of Submerged Water Well PumpsSubmerged water well pumps can be used in diverse water management applications, including:1. Domestic Water Supply: Submerged pumps can be used to supply water to households for domestic needs, such as cooking, bathing, and laundry.2. Commercial and Industrial Water Supply: Submerged pumps can be used in commercial and industrial applications, such as supplying water to office buildings, factories, and irrigation systems.3. Water Supply for Livestock: Submerged pumps can be used to supply water to livestock, such as cows, horses, and sheep, in rural areas where access to water is limited.ConclusionSubmerged water well pumps offer numerous benefits compared to other types of water pumps, including high efficiency, low noise, longevity, and energy efficiency. These pumps are highly versatile and can be used in diverse water management applications, ranging from domestic water supply to commercial and industrial water supply. As China continues to invest in water pump technology, we can expect to see even more innovative solutions that cater to the diverse needs of water management.
High-Quality Mud Pumps for Effective Drilling in China
The global market for mud pumps for drilling operations is witnessing a significant rise in demand, driven by the growing number of drilling activities globally. As one of the leading manufacturers and suppliers of mud pumps for drilling operations, {Company Name} is poised to capitalize on this increasing demand with its high-quality products.{Company Name} has earned a reputation for excellence within the industry, offering a wide range of mud pumps that are designed to meet the needs of drilling operations in various environments. The company excels in providing reliable and efficient solutions for both onshore and offshore drilling applications, making it a preferred choice for many drilling companies around the world.One of the key products offered by {Company Name} is its China Mud Pump, which has garnered attention for its superior performance and durability. The China Mud Pump is designed to withstand the harsh conditions typically encountered in drilling operations, making it a reliable and cost-effective choice for operators. With a strong focus on quality and reliability, {Company Name} has established itself as a trusted partner for companies seeking high-performance mud pumps for their drilling activities.In addition to the China Mud Pump, {Company Name} also offers a comprehensive range of mud pumps for drilling operations. These products are designed to meet the specific requirements of different drilling environments, providing operators with the flexibility to choose the right solution for their needs. With a commitment to innovation and continuous improvement, {Company Name} ensures that its mud pumps are equipped with the latest technologies to deliver optimal performance and reliability.The company's dedication to quality and customer satisfaction is reflected in its rigorous testing and certification processes. Each mud pump undergoes thorough testing to ensure compliance with industry standards and regulations, giving customers the assurance that they are investing in a reliable and safe product. With a strong focus on customer service, {Company Name} also offers comprehensive support and after-sales services to assist customers in maximizing the performance and lifespan of their mud pumps.As the global demand for energy continues to grow, the need for efficient and reliable drilling equipment has become increasingly important. {Company Name} recognizes the significance of its role in supporting the drilling industry, and is committed to developing innovative solutions that empower operators to achieve their objectives with confidence. By continually investing in research and development, the company aims to stay ahead of the curve in offering cutting-edge mud pumps that deliver superior performance and value.In conclusion, {Company Name} is well-positioned to meet the rising demand for mud pumps for drilling operations, with its high-quality products and commitment to customer satisfaction. With a strong track record of reliability and performance, the company is a trusted partner for drilling companies seeking reliable and efficient solutions for their operations. As the global drilling industry continues to evolve, {Company Name} remains dedicated to delivering innovative and dependable mud pumps that empower operators to achieve their goals safely and efficiently.
Top Quality Screen Mesh and Screen for Various Industries in China
China Screen Mesh and Screen Company, known for its high-quality and durable screen products, has recently announced the launch of a new and improved screen mesh designed to meet the specific needs of various industries. The company, which has been a leader in the screen manufacturing industry for over a decade, has consistently provided innovative and reliable solutions to its customers, and the new mesh is a testament to its commitment to delivering top-notch products.The new screen mesh is constructed using advanced materials and technology, ensuring superior strength and durability. It is designed to withstand harsh environmental conditions, making it suitable for a wide range of applications, including mining, construction, agriculture, and pharmaceuticals. The mesh is available in various sizes and configurations, allowing for customization to meet the specific requirements of different industries.One of the key features of the new screen mesh is its high tensile strength, which enables it to effectively withstand heavy loads and abrasive materials. This makes it ideal for use in mining and construction, where the screens are often subjected to extreme wear and tear. The mesh also offers excellent resistance to corrosion, ensuring long-lasting performance in outdoor and industrial environments.In addition to its physical properties, the new screen mesh is also designed for easy installation and maintenance. Its modular design allows for quick and hassle-free replacement, reducing downtime and increasing productivity. The company has also developed a range of accessories and support systems to facilitate the installation and use of the mesh, further enhancing its overall usability.The launch of the new screen mesh is a result of China Screen Mesh and Screen Company's continuous research and development efforts. The company has a dedicated team of engineers and technicians who are constantly striving to improve and innovate its product offerings. By leveraging the latest technologies and materials, the company is able to stay ahead of the competition and provide cutting-edge solutions to its customers.The company's commitment to quality and customer satisfaction has earned it a strong reputation in the industry. Its products are trusted by businesses and organizations around the world, and the new screen mesh is expected to further solidify its position as a leading provider of screen solutions. With a focus on performance, reliability, and innovation, China Screen Mesh and Screen Company continues to set the bar for the industry.In addition to its product offerings, the company also provides comprehensive technical support and customer service. Its team of experts is available to assist customers with product selection, installation, and troubleshooting, ensuring a seamless experience from start to finish. This level of support has helped the company build long-lasting relationships with its clients and establish itself as a trusted partner in the industry.As China Screen Mesh and Screen Company continues to grow and expand its product line, it remains committed to upholding its core values of quality, innovation, and customer satisfaction. The launch of the new screen mesh is just one example of the company's dedication to providing top-of-the-line solutions to its clients. With its proven track record and forward-thinking approach, China Screen Mesh and Screen Company is poised to remain a driving force in the screen manufacturing industry for years to come.
Top Quality Screen Mesh for Various Applications
China Screen Mesh and Screen (CSMS) is a well-known company in the industry, specializing in the production and distribution of high-quality screen mesh and screens. With years of experience and a commitment to excellence, CSMS has become a trusted name in the market, providing solutions for various industries including mining, construction, and agriculture.The company offers a wide range of products, including woven wire mesh, welded wire mesh, and polyurethane screen. These products are designed to meet the specific needs of customers, offering durability, reliability, and superior performance in demanding conditions. Whether it's for screening and sizing, filtering, or protection, CSMS has the right solution for every application.One of the key factors that sets CSMS apart from its competitors is its dedication to product quality. The company has established a strict quality control system, ensuring that every product that leaves its facility meets the highest standards. From the selection of raw materials to the manufacturing process and final inspection, CSMS is committed to delivering products that exceed customer expectations.In addition to quality, CSMS also prides itself on its ability to provide customized solutions. The company understands that every customer has unique requirements, and its team of experienced engineers and technicians is always ready to work closely with clients to develop tailored products that address specific challenges. This personalized approach has earned CSMS a reputation for being a reliable partner in the industry.Furthermore, CSMS places great importance on innovation and technology. The company continuously invests in research and development to improve its products and processes, staying ahead of the curve in a rapidly evolving market. By leveraging the latest advancements in materials and manufacturing techniques, CSMS is able to offer cutting-edge solutions that deliver exceptional performance and value.Apart from its commitment to product excellence, CSMS also places a strong emphasis on customer satisfaction. The company strives to build long-term relationships with its clients, offering comprehensive support and service throughout the entire customer journey. From initial consultation to after-sales support, CSMS is dedicated to ensuring that every customer has a positive experience.Looking ahead, CSMS is poised to expand its presence in the global market. With a strong foundation built on quality, innovation, and customer focus, the company is well-positioned to seize new opportunities and overcome challenges. By staying true to its core values and leveraging its strengths, CSMS is ready to write the next chapter of its success story.In conclusion, China Screen Mesh and Screen (CSMS) is a leading provider of high-quality screen mesh and screens, with a strong focus on product quality, customization, innovation, and customer satisfaction. With a proven track record and a clear vision for the future, CSMS is set to continue its growth and make a lasting impact in the industry.