Efficient Mud Cleaning Machine for Improved Operation
By:Admin
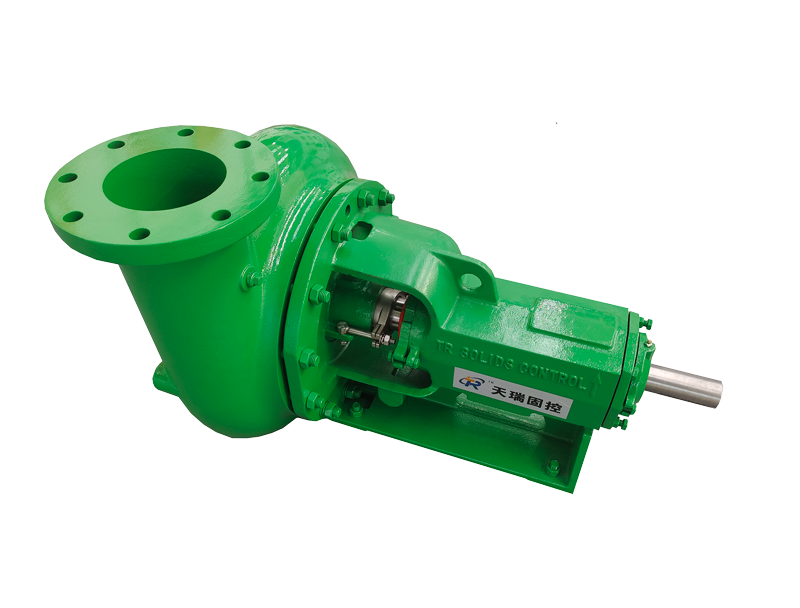
The oil and gas industry is constantly evolving, with new technologies and innovations that aim to improve efficiency and reduce environmental impact. One such innovation that is making waves in the industry is the Mud Cleaning Machine, a game-changing technology that is revolutionizing the way drilling mud is treated and recycled.
The Mud Cleaning Machine, developed by a leading oilfield equipment manufacturer, is a state-of-the-art piece of equipment that is designed to separate and remove solids from drilling mud, resulting in cleaner mud that can be reused in the drilling process. This innovative technology is helping oil and gas companies to significantly reduce the amount of drilling waste that is generated, ultimately leading to cost savings and a smaller environmental footprint.
The Mud Cleaning Machine works by utilizing a series of screens and hydrocyclones to remove solids from the drilling mud, while also separating the mud into different density levels. The cleaned mud can then be reused in the drilling process, reducing the need for fresh mud and ultimately lowering the overall cost of drilling operations.
In addition to its environmental and cost-saving benefits, the Mud Cleaning Machine is also improving the safety of drilling operations. By removing solids from the mud, the risk of equipment damage and downtime is significantly reduced, leading to smoother and more efficient drilling operations.
The company behind the Mud Cleaning Machine has a long-standing reputation for developing and manufacturing high-quality oilfield equipment. With a focus on innovation and a commitment to sustainability, the company has become a trusted partner for oil and gas companies around the world.
In addition to the Mud Cleaning Machine, the company also offers a range of other equipment and services designed to improve the efficiency and environmental performance of drilling operations. From wastewater treatment systems to solid control equipment, the company provides a comprehensive suite of solutions that are helping oil and gas companies to meet their operational and sustainability goals.
The development of the Mud Cleaning Machine is a testament to the company’s dedication to innovation and its commitment to driving positive change in the oil and gas industry. By providing a solution that not only improves efficiency and cost savings but also reduces environmental impact, the company is playing a crucial role in helping the industry to become more sustainable and responsible.
Furthermore, the company’s dedication to quality and customer satisfaction sets it apart from its competitors. With a global network of sales and service locations, the company is able to provide ongoing support to its customers, ensuring that they are able to maximize the value and performance of the Mud Cleaning Machine and other equipment.
The impact of the Mud Cleaning Machine on the oil and gas industry is undeniable. By enabling companies to reduce waste, improve efficiency, and enhance safety, this innovative technology is helping to shape the future of drilling operations. As the industry continues to evolve, it is clear that the Mud Cleaning Machine will play a crucial role in driving positive change and creating a more sustainable and responsible oil and gas industry.
Company News & Blog
Mastering the Art of Efficient Drilling with Advanced Drilling Machines
Title: Revolutionary Drilling Machine Revolutionizes the IndustryIntroduction:In a groundbreaking development, a leading company in the manufacturing sector has unveiled an innovative Drilling Machine that is set to transform drilling operations across industrial sectors worldwide. This cutting-edge technology is poised to minimize costs, increase efficiency, and enhance precision, placing the company at the forefront of the drilling industry.Body:1. Redefining the Drilling Industry:The newly introduced Drilling Machine marks a significant breakthrough in the industry, promising to revolutionize the way drilling operations are conducted. Built upon cutting-edge technology and the latest industry know-how, this innovative solution sets itself apart by offering unmatched drilling efficiency and precision.2. Enhanced Efficiency and Productivity:The advanced features of the Drilling Machine are designed to streamline operations and optimize productivity. Incorporating powerful motors and state-of-the-art control mechanisms, this machine can perform drilling tasks with unrivaled speed and accuracy. Additionally, its automated functions and intelligent control system minimize the need for manual intervention, ensuring seamless and efficient operations.3. Precision Engineering at its Best:Precision is paramount in drilling operations, and this Drilling Machine does not disappoint. Equipped with high-precision sensors and advanced guidance systems, it allows for drilling operations to be conducted with utmost accuracy. This not only reduces the risk of errors but also ensures consistent quality and reliability in creating holes of varying depths and diameters.4. Diverse Applications across Industries:With its versatility and adaptability, the Drilling Machine finds application across a range of industries. From construction and manufacturing to oil and gas exploration, this innovative solution caters to the diverse needs of different sectors, offering a comprehensive drilling solution that meets the highest industry standards.5. Cost-Effective and Sustainable:This state-of-the-art Drilling Machine not only improves efficiency but also promotes sustainability. It integrates energy-saving features that help reduce power consumption, making it an environmentally friendly choice for companies looking to lower their carbon footprint. Moreover, its durability and resilience ensure minimal maintenance costs and long-term operational effectiveness.6. Ensuring Workplace Safety:The design of the Drilling Machine prioritizes safety as a fundamental aspect. With built-in safety features such as emergency stop buttons, safety alarms, and automatic shut-off mechanisms, operators can carry out drilling tasks confidently and safely. This focus on workplace safety is essential to protect workers and prevent accidents in high-risk environments.7. Revolutionizing Drilling Operations:The implementation of this advanced Drilling Machine is set to revolutionize drilling operations in the industry. Companies within various sectors can look forward to substantial improvements in efficiency, cost-savings, and productivity. Additionally, the focus on precision and safety ensures that end-products meet or exceed the highest quality standards.Conclusion:The introduction of the innovative Drilling Machine is a testimony to the continual advancements in the manufacturing sector. By marrying cutting-edge technology with precision engineering, the company has successfully developed a game-changing solution that is set to redefine the drilling industry. With its unrivaled efficiency, precision, and focus on safety, this Drilling Machine promises to transform drilling operations across numerous industries, bolstering productivity and sustainability while reducing costs.
Highly Efficient Shear Mixing Technology for Industrial Applications
Today, we are excited to introduce a new cutting-edge shear mixer that is set to revolutionize the industry. This innovative piece of equipment, which combines state-of-the-art technology with high-quality manufacturing, (brand name removed) has been designed to meet the diverse needs of our customers and provide an unparalleled level of performance.At (company name removed), we have been at the forefront of the industry for many years, and our commitment to innovation and excellence has made us a trusted name in the market. Our aim has always been to provide our customers with the most advanced and reliable equipment, and the new shear mixer is the latest example of our dedication to that goal.This shear mixer has been meticulously engineered to deliver exceptional results across a wide range of applications. Its advanced design allows for precise control over the mixing process, ensuring a consistent and uniform blend every time. Whether it is used in the food and beverage industry, pharmaceuticals, or chemical processing, this shear mixer is capable of meeting the most demanding requirements with ease.One of the standout features of this shear mixer is its versatility. With the ability to handle a variety of viscosities and accommodate different batch sizes, it is a truly adaptable piece of equipment that can be tailored to the specific needs of our customers. This level of flexibility not only increases efficiency but also minimizes downtime, ultimately leading to cost savings and improved productivity.In addition to its outstanding performance, this shear mixer has been designed with the user in mind. Its intuitive interface and user-friendly controls make it easy to operate, while its robust construction ensures long-term reliability. Furthermore, its compact footprint means that it can be easily integrated into existing production lines, making it a seamless addition to any facility.The introduction of this shear mixer represents a significant milestone for (company name removed) and reinforces our commitment to pushing the boundaries of what is possible in the industry. With its advanced technology, unmatched performance, and user-focused design, we are confident that it will set a new standard for shear mixing equipment.In conclusion, the new shear mixer from (company name removed) represents a leap forward in shear mixing technology. With its unparalleled performance, versatility, and user-friendly design, it is poised to revolutionize the industry and provide our customers with a superior mixing solution. We are proud to add this exceptional piece of equipment to our portfolio, and we are excited about the positive impact it will have on the businesses of our customers.
The latest innovation in centrifugal impeller technology unveiled
Centrifugal Impeller Revolutionizing Industrial Applications: A Game Changer byIn today's fast-paced industrial world, efficiency and innovation are key factors that drive success. One such innovation that is revolutionizing industrial applications is the Centrifugal Impeller. This state-of-the-art technology is a game-changer in the field of industrial equipment, setting new standards for performance and reliability.The Centrifugal Impeller, developed by a leading industrial equipment manufacturer, is designed to meet the growing demands of various industries, including aerospace, automotive, energy, and HVAC. Its advanced engineering and precision manufacturing make it an ideal choice for applications that require high efficiency, low noise, and long-term reliability.One of the key features of the Centrifugal Impeller is its unique blade design, which is optimized for maximum performance. This design allows for efficient airflow and pressure generation, making it suitable for a wide range of industrial processes. Whether it's for air handling, combustion, or cooling systems, the Centrifugal Impeller delivers unmatched performance, making it a versatile solution for modern industrial applications.Furthermore, the Centrifugal Impeller is also known for its durability and long service life. Its robust construction and high-quality materials ensure that it can withstand the rigors of industrial operations, making it a cost-effective investment for businesses. With minimal maintenance requirements, the Centrifugal Impeller offers a hassle-free solution for industrial equipment needs.In addition to its performance and reliability, the Centrifugal Impeller is also designed with energy efficiency in mind. Its aerodynamic design and precise manufacturing processes enable it to achieve high levels of efficiency, reducing energy consumption and operating costs for businesses. This makes it an environmentally friendly choice for industrial applications, contributing to sustainability efforts in various industries.The company behind the Centrifugal Impeller takes pride in its commitment to quality and innovation. With a team of experienced engineers and experts in industrial equipment, the company has a proven track record of delivering cutting-edge solutions that meet the evolving needs of modern industries. By continuously investing in research and development, the company ensures that its products, including the Centrifugal Impeller, are at the forefront of technological advancements.Furthermore, the company's dedication to customer satisfaction sets it apart in the industry. From initial consultation to product delivery and after-sales support, the company places a strong emphasis on understanding and meeting the specific requirements of its clients. With a focus on building long-term partnerships, the company strives to exceed customer expectations and provide tailored solutions that add value to businesses.As the industrial landscape continues to evolve, the demand for innovative and reliable equipment remains high. The Centrifugal Impeller is a testament to the impact of advanced technology in meeting these demands, offering a solution that enhances efficiency, performance, and sustainability for industrial applications. With its cutting-edge design, durability, and energy efficiency, the Centrifugal Impeller is poised to shape the future of industrial equipment and set new standards for excellence in the industry.
High-performance Shale Shaker for Oil and Gas Industry
Mongoose Pro Shale Shaker Sets the Standard for Efficiency and Reliability in Shale Shaker TechnologyThe demand for shale shaker technology has been steadily rising in the oil and gas industry, and companies are consistently looking for the most efficient and reliable equipment to meet their needs. This is where the Mongoose Pro Shale Shaker comes in, setting the standard for efficiency and reliability in shale shaker technology.The Mongoose Pro Shale Shaker is a product of innovation and expertise, developed by a leading company in the oil and gas industry. With a commitment to providing top-of-the-line equipment, this company has a proven track record of delivering high-quality products that are designed to meet the demands of the ever-evolving industry.This particular shale shaker is built to withstand the harshest drilling conditions, making it the perfect choice for companies looking to maximize their drilling operations. With its advanced design and cutting-edge technology, the Mongoose Pro Shale Shaker is able to effectively separate solids from drilling fluid, resulting in improved efficiency and reduced operating costs.One of the key features of the Mongoose Pro Shale Shaker is its adjustable G-force, allowing for optimal performance in various drilling conditions. This, in combination with its high-capacity composite screen panels, ensures that the shaker is able to handle a wide range of drilling fluids and produce consistently high-quality results.In addition to its impressive performance capabilities, the Mongoose Pro Shale Shaker is also built with ease of use in mind. Its user-friendly interface and simple maintenance requirements make it an ideal choice for companies looking to streamline their operations and maximize productivity.The Mongoose Pro Shale Shaker is also designed with durability in mind, with rugged construction and high-quality materials that are built to last. This ensures that companies can rely on this equipment to perform consistently, even in the most challenging drilling environments.Furthermore, the Mongoose Pro Shale Shaker is backed by a team of experts who are dedicated to providing top-notch service and support to ensure that customers get the most out of their investment. This level of support is a testament to the company's commitment to customer satisfaction and its dedication to delivering reliable equipment that meets the needs of the industry.Overall, the Mongoose Pro Shale Shaker is a game-changer in the world of shale shaker technology, offering unmatched efficiency, reliability, and performance. With its advanced design, user-friendly interface, and durable construction, it is the ideal choice for companies looking to maximize their drilling operations and achieve optimal results.As the demand for shale shaker technology continues to grow, the Mongoose Pro Shale Shaker stands out as a leader in the industry, providing companies with the equipment they need to stay ahead of the curve. With its proven track record of delivering high-quality products and exceptional customer support, this company is setting the standard for excellence in shale shaker technology.
High-Quality Drilling Rig Parts and Drawworks in China
China has long been a leader in the oil and gas industry, and their advancements in drilling rig technology have been at the forefront of this. With a commitment to innovation and quality, Chinese companies continue to provide essential parts and equipment for drilling operations around the world.One such company is {}, a leading provider of drilling rig parts and equipment. With a focus on research and development, they have become known for their high-quality products that meet the demands of the industry. From drill drawworks to drilling rig components, {} has established itself as a reliable supplier for companies looking to enhance their drilling operations.In recent years, the demand for drilling rig parts and equipment has continued to grow as the global energy market expands. This has led to increased competition among suppliers, but {} has been able to distinguish itself through its dedication to quality and customer service.One of the key products that {} offers is their drill drawworks. This essential component of a drilling rig is responsible for raising and lowering the drill string, making it a vital part of the overall operation. With a focus on durability and efficiency, {}'s drill drawworks have become a popular choice for companies looking to maximize their drilling capabilities.In addition to drill drawworks, {} also provides a wide range of other drilling rig parts, including mud pumps, top drives, and more. Their comprehensive selection of products makes them a one-stop shop for companies in need of reliable equipment for their drilling operations.One of the major advantages of working with {} is their commitment to customization. They understand that every drilling operation is unique, and they are able to tailor their products to fit the specific needs of their customers. This flexibility has made them a preferred supplier for drilling companies around the world.In addition to their product offerings, {} also provides comprehensive support and services for their customers. This includes technical assistance, maintenance and repair services, and training programs for operators. This commitment to customer satisfaction sets {} apart from other suppliers and has helped them build long-lasting relationships with their clients.With an eye towards the future, {} continues to invest in research and development to further enhance their products and services. They understand the importance of staying ahead of the curve in an ever-evolving industry, and they are dedicated to maintaining their position as a leading supplier of drilling rig parts and equipment.As the global demand for energy continues to rise, the importance of reliable drilling operations has never been greater. Companies like {} play a critical role in supporting these operations by providing high-quality parts and equipment that are essential for success. With their commitment to innovation and customer satisfaction, {} is well-positioned to continue leading the way in the drilling rig industry for years to come.
New Mixing Hopper Technology Offers Improved Efficiency
Venturi Mixing Hopper, an innovative solution for efficient material mixing, has rapidly gained popularity in the manufacturing industry. This technology has revolutionized the way materials are mixed, ensuring a consistent and homogeneous blend for various applications. The Venturi Mixing Hopper is designed and manufactured by a leading company that specializes in providing solutions for material handling and processing.{Company Name} has been at the forefront of manufacturing innovative equipment for the materials industry for over two decades. The company is dedicated to providing high-quality solutions that optimize material handling processes and improve overall operational efficiency. With a team of experienced engineers and experts, {Company Name} has continuously strived to develop cutting-edge technologies that meet the evolving needs of its customers.The Venturi Mixing Hopper is one such innovative product that has been designed to address the challenges associated with traditional material mixing methods. The technology is based on the Venturi effect, which involves the use of a converging-diverging nozzle to create a low-pressure zone that draws in and mixes the materials. This unique design ensures thorough and efficient mixing, with minimal energy consumption.One of the key features of the Venturi Mixing Hopper is its ability to handle a wide range of materials, including powders, granules, and other bulk solids. This versatility makes it an ideal solution for various industries, such as food processing, pharmaceuticals, chemicals, and construction. The technology can be customized to meet specific requirements, ensuring that it can effectively mix materials of different particle sizes and densities.In addition to its versatility, the Venturi Mixing Hopper offers several other benefits that contribute to its growing popularity in the industry. The technology is known for its rapid mixing capabilities, allowing for a quick and efficient blending process. This not only saves time but also reduces the overall production costs.Furthermore, the Venturi Mixing Hopper is designed to minimize material segregation and degradation, ensuring that the integrity of the blend is maintained throughout the process. This is particularly important for industries that require precise and consistent material mixtures, such as pharmaceutical manufacturing.Another key advantage of the Venturi Mixing Hopper is its compact design and ease of integration into existing production lines. The technology is engineered to be space-efficient, making it suitable for both new installations and retrofits. Its user-friendly interface and automated operation further simplify its use, minimizing the need for manual intervention and oversight.The Venturi Mixing Hopper is also designed with durability and reliability in mind, ensuring minimal maintenance requirements and long-term performance. This makes it a cost-effective solution for businesses looking to improve their material mixing processes without incurring excessive operational expenses.As the demand for efficient material mixing solutions continues to grow, the Venturi Mixing Hopper has emerged as a game-changer in the industry, offering a reliable and sustainable solution for businesses of all sizes. Its innovative design and advanced capabilities have positioned it as a leading technology in the field of material handling and processing, catering to the evolving needs of the modern manufacturing landscape.With a proven track record of delivering high-quality solutions, {Company Name} has established itself as a trusted partner for businesses seeking to enhance their material handling processes. The company's commitment to innovation and customer satisfaction has driven the development of technologies like the Venturi Mixing Hopper, setting new standards for performance and efficiency in the industry.In conclusion, the Venturi Mixing Hopper represents a significant advancement in material mixing technology, offering a reliable and efficient solution for businesses across various industries. With its unique design, versatility, and numerous benefits, this innovative technology has cemented its position as a leading solution for material handling and processing. {Company Name} continues to be a driving force behind the advancement of such groundbreaking technologies, further solidifying its reputation as a pioneer in the industry.
Maximizing Cost-Effectiveness for Horizontal Directional Drilling Projects: Considerations for Drilling Rigs and Mud Solids Control Systems
Title: Innovations in Horizontal Directional Drilling Rig and Mud Solids Control Systems in ChinaIntroduction:China is witnessing significant advancements in the field of horizontal directional drilling (HDD) rigs and mud solids control systems. With the joint venture between international companies like Vermeer and local manufacturers such as GN Desander Desilter and Drillto, China is becoming a leading player in the HDD market. This article will explore the latest innovations in HDD technology and the importance of balancing budget and quality for maximum effectiveness.Vermeer Navigator HDD Drilling Rig:The Vermeer Navigator series of HDD drills and units are known for their exceptional performance in the underground installation of utilities. These rigs are widely used for gas, electric, water, telecommunication, and soil remediation projects without the need for extensive excavation or trenching. Vermeer's technology ensures accurate and efficient drilling, making it an ideal choice for a wide range of HDD applications.Drillto HDD Machines:Established in 1999, Drillto Trenchless Co., Ltd. is a civilian-owned science-technology enterprise specializing in the research and development of no-dig technology. With Mr. Pengwang leading the team, Drillto has emerged as the fastest-growing HDD machine manufacturer globally. The company boasts a state-of-the-art manufacturing facility equipped with advanced machinery like EDM and CNC Lathe. Their expertise lies in manufacturing HDD rigs, drill pipes, and representing renowned brands in the field.Balancing Budget and Quality:While undertaking an HDD project, achieving the right balance between budget and quality is crucial. By opting for world-renowned manufacturers like Vermeer or their joint venture companies in China, project managers can ensure the use of high-quality drilling rigs. These rigs are designed to offer reliability, efficiency, and accuracy in underground installations, thereby reducing overall project costs.Furthermore, selecting a reliable mud solids control system is equally significant in HDD projects. GN solids control, a reputable supplier in the industry, is highly regarded for its efficient drilling mud processing solutions. Their HDD mud systems have gained recognition from clients worldwide and are being successfully deployed on various projects. By partnering with GN solids control, project managers can achieve optimal drilling performance while maintaining strict quality standards and cost-effectiveness.Conclusion:The horizontal directional drilling industry in China is witnessing remarkable growth with companies like Vermeer, GN Desander Desilter, and Drillto leading the way. With their innovative technologies and focus on quality, these companies are transforming the HDD landscape. Balancing budget and quality is a critical factor for the success of any HDD project. By choosing renowned drilling rig manufacturers and reliable mud solids control system suppliers like GN solids control, project managers can achieve maximum effectiveness while reducing costs.
Hand Operated Centrifuge and Drilling Mud Tester in China
China-based company, X, has recently launched a revolutionary hand-operated centrifuge and drilling mud tester, which is set to make a significant impact in the drilling industry. This innovative technology is designed to provide accurate and reliable testing of drilling mud, ensuring the efficiency and safety of drilling operations.The hand-operated centrifuge and drilling mud tester is a portable and easy-to-use device, which can be operated manually without the need for any external power source. This makes it an ideal tool for use in remote locations or in areas where access to electricity is limited.The centrifuge component of the device is capable of separating different components of the drilling mud, such as solid particles and liquids, with great precision. This allows for thorough analysis of the mud, enabling users to identify any potential issues or contamination that may affect the drilling process.Furthermore, the drilling mud tester is equipped with advanced sensors and measurement tools, which provide accurate data on the viscosity, density, and other key properties of the drilling mud. This information is crucial for ensuring the stability and effectiveness of the drilling operation.The hand-operated centrifuge and drilling mud tester is the result of extensive research and development by X, a leading manufacturer of drilling equipment and tools. With a strong focus on innovation and quality, the company has established itself as a trusted provider of cutting-edge solutions for the drilling industry.X has a proven track record of delivering reliable and efficient products to its customers, and the hand-operated centrifuge and drilling mud tester is no exception. The device is built to withstand the harsh conditions of drilling operations, with rugged construction and durable materials that ensure long-lasting performance.Furthermore, X provides comprehensive training and support for its products, ensuring that customers are able to make the most of their investment. The company’s team of technical experts is available to provide guidance on the operation and maintenance of the hand-operated centrifuge and drilling mud tester, as well as any other products in their extensive lineup.In addition to its commitment to quality and customer support, X is also dedicated to the implementation of sustainable and environmentally friendly practices in its operations. The hand-operated centrifuge and drilling mud tester is designed with this in mind, with energy-efficient features and a minimal environmental footprint.As a result of its numerous advantages and benefits, the hand-operated centrifuge and drilling mud tester is expected to be well-received by drilling companies and professionals around the world. Its portability, ease of use, and accurate testing capabilities make it an indispensable tool for ensuring the success of drilling operations.In conclusion, the launch of the hand-operated centrifuge and drilling mud tester by X represents a significant advancement for the drilling industry. With its innovative technology, robust construction, and comprehensive support, this device is set to become a vital asset for drilling companies and professionals seeking to enhance the efficiency and safety of their operations. X continues to demonstrate its commitment to delivering superior solutions for the drilling industry, and the hand-operated centrifuge and drilling mud tester is a prime example of this dedication.
Efficient Waste Decanter Centrifuge Enhances Solid-Liquid Separation
Waste Decanter Centrifuge Technology Revolutionizes Industrial Waste ManagementAs industries continue to thrive and expand, the amount of industrial waste continues to rise. Industrial waste is defined as the residue of manufacturing, construction, and industrial processes, including hazardous waste that requires special handling and disposal. With experts predicting that global industrial waste will double by 2025, it is time for companies to take action. The solution to this problem lies in proper waste management techniques such as decanter centrifuges, and one company that has proved its mettle in this field is (company name).The decanter centrifuge is a highly effective piece of equipment in separating solid and liquid materials from waste. Achieving solid-liquid separation is essential to the waste disposal process as it allows for the proper disposal of the liquid phase and minimizes disposal costs. This process can be achieved through a combination of sedimentation and centrifugation, with the decanter centrifuge being the most effective means of achieving this. The centrifugal force created in the equipment allows for the separation of heavier materials from lighter ones, with the resulting liquid and solid phases easily collected and disposed of separately.Established in (year), (company name) is a leading manufacturer of industrial decanter centrifuges. They provide state-of-the-art and environmentally friendly solutions for various applications worldwide. Their commitment to developing and manufacturing green technologies that promote sustainable industrial growth has seen them earn a reputation as a respected leader in the waste management industry.The company's products are widely used in several industries such as wastewater treatment, food and beverage processing, pharmaceuticals, and mining, among others. With a focus on innovation, efficiency, and quality, their industrial decanter centrifuge technology presents users with several advantages such as increased productivity, reduced maintenance costs, and safer, cleaner products.One of the key benefits of (company name)'s equipment is its flexibility. The decanter centrifuge can be used in a wide range of products, including slurries, slurries containing high solids, and even recovering valuable oils from drilling mud. The process is simplified and straightforward, with just one operator required to operate the machine and monitor its performance.One of the significant challenges of industrial waste management is the variety of waste materials generated. The waste varies in composition, viscosity, and particle size, among other factors. To address this challenge, the company has designed and developed different types of decanter centrifuges suitable for a wide range of waste types and applications. This modular and versatile design ensures that clients have access to the most effective and efficient decanter centrifuge technology applicable to their specific industry, resulting in cost savings and improved operational efficiencies.Another innovative feature of (company name)'s decanter centrifuge equipment is its automation capabilities. The equipment comes equipped with advanced sensors that allow for real-time monitoring of the operating parameters. This feature enables operators to troubleshoot any issues promptly, resulting in fewer downtimes and increased uptime. Additionally, the automated systems provide predictive maintenance that helps extend the lifespan of the equipment and reduces maintenance costs.The demand for effective and sustainable waste management solutions is growing. Industries and regulators alike are pushing for more eco-friendly solutions that promote sustainable industrial growth. Orderly and safe waste disposal is not only a legal requirement, but it also promotes responsible corporate citizenship. By using (company name)'s decanter centrifuge technology, industries can play their role in promoting these values while at the same time enjoying increased efficiency, reduced costs, and peace of mind.In conclusion, (company name)'s decanter centrifuges provide industries with an environmentally conscious solution for industrial waste disposal. Through a combination of expert engineering and innovative technology, the company has managed to design a range of highly efficient, versatile and cost-effective decanter centrifuge equipment that is adaptable to a wide range of waste types and applications. With their superior customer support and quality equipment, (company name) offers industrial clients the best solution for their industrial waste management needs. The company has truly revolutionized the waste management industry with their highly effective and environmentally friendly decanter centrifuge technology, and will continue to lead the way in green industrial growth.
Highly Efficient Glass Washing and Drying Machines from China for All Your Needs
China Glass Washing Machine and Glass Washing and Drying Machine have been making headlines in the industry recently, as their advanced technology and high-quality performance continue to impress customers. With a commitment to innovation and customer satisfaction, these machines are becoming increasingly popular in the global market.China Glass Washing Machine is a leading manufacturer of glass processing equipment, specializing in the production of glass washing machines. These machines are designed to effectively clean glass surfaces, removing dirt, dust, and other impurities to ensure a spotless finish. With their advanced technology and precise control systems, China Glass Washing Machine has set a new standard for glass washing equipment.Similarly, Glass Washing and Drying Machine has made a name for itself as a top-tier supplier of glass processing machinery. The company's glass washing and drying machines are known for their exceptional performance and reliability. With a focus on quality and efficiency, Glass Washing and Drying Machine has become a trusted partner for businesses looking to enhance their glass processing capabilities.One of the key factors contributing to the success of these machines is the use of advanced technology. China Glass Washing Machine and Glass Washing and Drying Machine have both incorporated cutting-edge features into their products, such as intelligent control systems and high-speed operation. These technological advancements have allowed the machines to deliver consistent and reliable results, meeting the rigorous demands of the industry.In addition to their technological innovations, both companies prioritize customer satisfaction. China Glass Washing Machine and Glass Washing and Drying Machine are committed to providing exceptional service and support to their clients. From initial consultation to after-sales maintenance, the companies strive to ensure a positive experience for their customers.Moreover, the machines are designed with sustainability in mind, incorporating energy-efficient solutions to minimize environmental impact. This dedication to sustainability aligns with the growing emphasis on eco-friendly practices in the industry, making China Glass Washing Machine and Glass Washing and Drying Machine a preferred choice for businesses seeking sustainable glass processing solutions.With a strong track record of performance and reliability, these machines have been embraced by customers around the world. From large-scale manufacturing facilities to small glass processing workshops, China Glass Washing Machine and Glass Washing and Drying Machine have made a significant impact on the industry.In conclusion, China Glass Washing Machine and Glass Washing and Drying Machine have emerged as leading providers of glass processing machinery, thanks to their advanced technology, commitment to customer satisfaction, and dedication to sustainability. As the demand for high-quality glass processing equipment continues to grow, these machines are well-positioned to meet the needs of the industry, setting a new standard for performance and innovation. With their impressive track record and a focus on continuous improvement, China Glass Washing Machine and Glass Washing and Drying Machine are poised to remain at the forefront of the industry for years to come.