Enhancing HDD Mud Pump Efficiency: Introducing a High-performance Mud Mixing Pump
By:Admin
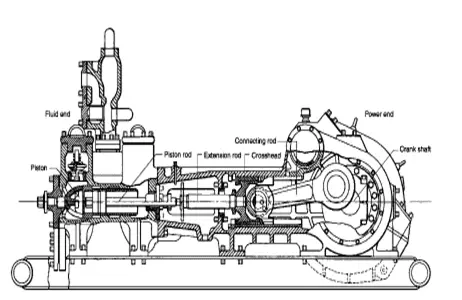
Introduction:
Horizontal directional drilling (HDD) has emerged as a key technique for the installation of underground utilities, minimizing disruptions to the surrounding environment. However, HDD projects require a well-designed mud recycling system to efficiently manage drilling fluids. In this regard, the mud mixing pump acts as a supercharging pump, revolutionizing the HDD mud pump system.
Compact and Convenient:
The HDD mud recycling system is typically a compact unit that is incredibly convenient for transportation. The integrated design allows for easy movement and ensures efficiency while relocating from one drilling site to another. Such systems are in high demand as they offer enhanced flexibility and versatility to HDD contractors.
Role of Mud Mixing Pump:
The mud mixing pump plays a crucial role in the HDD mud pump system. Acting as a supercharging pump, it enhances the performance and efficiency of the whole operation. By mixing the drilling fluids with precision, it ensures optimal mud viscosity, density, and stability, thereby improving the overall drilling process.
Efficient Drilling Fluid Mixing:
With the integration of a mud mixing pump, HDD contractors can experience efficient drilling fluid mixing like never before. This equipment utilizes advanced technology to combine the different materials, chemicals, and additives required in drilling fluids. The precise and rapid mixing capability guarantees a consistent mud mixture, enabling contractors to maintain stability throughout the drilling process.
Enhanced Mud Recycling:
The mud mixing pump significantly contributes to enhancing the mud recycling process in HDD projects. By efficiently incorporating various additives, it ensures that the recovered drilling fluids are of excellent quality and can be reused effectively. This not only reduces operational costs but also minimizes the environmental impact of HDD activities.
Supreme Performance and Reliability:
The selection of a reliable and high-performance mud mixing pump is crucial for the success of an HDD project. Manufacturers like {Mud Cleaner Drilling} are renowned for their cutting-edge technology and innovative solutions in this field. With expertise in designing and manufacturing mud mixing pumps, they offer top-of-the-line equipment that meets the diverse requirements of HDD contractors.
Customized Solutions:
With a focus on customer satisfaction, companies specializing in mud mixing pumps provide tailored solutions to meet specific project needs. These solutions encompass a range of features, such as automated controls, user-friendly interfaces, and robust components, to ensure smooth operations and maximum efficiency during HDD projects.
Industry Impact:
The integration of the mud mixing pump into the HDD mud system has had a profound impact on the industry. By enhancing the mud recycling process and improving drilling fluid properties, it has significantly increased drilling speed, reduced downtime, and minimized waste. This cutting-edge equipment has revolutionized the efficiency and environmental sustainability of HDD projects worldwide.
Conclusion:
The mud mixing pump has emerged as a game-changer in the HDD industry, acting as a supercharging pump for the mud pump system. With its efficient drilling fluid mixing capabilities and potential for customization, this equipment has transformed the way HDD projects are executed. With technological advancements and the expertise of companies like {Mud Cleaner Drilling}, the future of HDD looks promising, ensuring improved performance, reduced costs, and greater environmental preservation.
Company News & Blog
Top Water Purifier and Treatment Solutions in China
China's leading water purification and water treatment company, with a strong focus on providing clean and safe drinking water for all, has been making waves in the industry with its innovative and high-quality products.With a reputation for excellence and a commitment to sustainability, the company has become a trusted name in the field of water purification. Their products are designed to remove impurities and contaminants from water, ensuring that it is safe for consumption and free from any harmful substances.One of the main reasons behind the company's success is its dedication to research and development. They employ a team of highly skilled and experienced professionals who are constantly working on improving their products and developing new technologies to better serve their customers.In addition to their innovative products, the company also places a strong emphasis on environmental responsibility. They strive to minimize their impact on the environment by using sustainable manufacturing practices and reducing their carbon footprint. This commitment to sustainability has earned them the respect and admiration of both customers and industry experts alike.The company's water purifiers and treatment systems are designed to meet the needs of a wide range of customers, from individual households to large-scale industrial applications. Their products are known for their reliability, efficiency, and durability, making them a popular choice for consumers and businesses alike.In recent years, the company has expanded its reach beyond the borders of China, exporting its products to countries around the world. This global expansion has further solidified their position as a leader in the water purification and treatment industry.One of the company's most notable achievements is its involvement in providing clean drinking water to areas affected by natural disasters and other humanitarian crises. Their portable water purification systems have been deployed in various disaster-stricken regions, providing vital support to communities in need.Looking ahead, the company remains committed to driving innovation and excellence in the field of water purification and treatment. They continue to invest in research and development, seeking to further improve their products and develop new solutions to address the ever-evolving challenges of water purification.In conclusion, China Water Purifier and Water Treatment is a company that has made a significant impact in the field of water purification and treatment. With their commitment to excellence, sustainability, and innovation, they have become a trusted name in the industry, both in China and around the world. As they continue to grow and expand, they are sure to set new standards for the industry and continue to provide clean and safe drinking water for all.
Fully Automatic Dry Priming Vacuum Assisted Pump and Automatic Dry Priming Pumps in China
China Fully Automatic Dry Priming Vacuum Assisted Pump and Automatic Dry Priming Pumps have been making waves in the industry, providing efficient and reliable solutions for various pumping needs. These innovative pumps have gained popularity for their advanced technology and high-performance capabilities.The fully automatic dry priming vacuum assisted pump is designed to handle tough pumping applications with ease. It is equipped with a powerful vacuum system that allows it to prime and re-prime automatically, without the need for manual intervention. This feature makes it ideal for use in dewatering, sewage bypass, and other challenging pumping scenarios. The pump's automatic self-priming capability ensures continuous operation, even in the most demanding conditions.In addition to the fully automatic dry priming vacuum assisted pump, the company also offers a range of automatic dry priming pumps that are designed for various industrial and municipal applications. These pumps are known for their reliability and efficiency, making them a preferred choice for customers across the globe. With their advanced design and innovative features, these pumps deliver superior performance and require minimal maintenance, making them a cost-effective solution for pumping needs.The company behind these cutting-edge pumps is a leading manufacturer of pumping solutions, with a strong focus on innovation and quality. With a history of over [X] years in the industry, they have established themselves as a trusted name in the global market. Their commitment to providing state-of-the-art pumping solutions has earned them a reputation for excellence and reliability.The company's fully automatic dry priming vacuum assisted pump and automatic dry priming pumps are the result of extensive research and development, aimed at meeting the evolving needs of their customers. These pumps are designed to deliver high performance, energy efficiency, and durability, ensuring that they meet the rigorous demands of modern pumping applications. Their dedication to quality and innovation sets them apart in the industry, making them a preferred choice for customers seeking reliable, high-performance pumping solutions.With a strong focus on customer satisfaction, the company prides itself on providing exceptional service and support to its customers. Their team of experienced professionals is dedicated to assisting customers in selecting the right pumping solutions for their specific needs, ensuring that they get the most out of their investment. Whether it's technical assistance, maintenance support, or troubleshooting, the company is committed to going the extra mile to ensure that their customers are satisfied with their products and services.In addition to their commitment to quality and customer satisfaction, the company also places a strong emphasis on environmental responsibility. Their pumps are designed to meet the highest standards of energy efficiency and eco-friendliness, helping to minimize their environmental impact. By choosing these pumps, customers can contribute to sustainable and responsible pumping practices, ensuring a greener future for generations to come.In conclusion, the company's fully automatic dry priming vacuum assisted pump and automatic dry priming pumps are revolutionizing the pumping industry with their advanced technology, reliability, and efficiency. With a strong focus on innovation, quality, and customer satisfaction, the company is setting new standards for pumping solutions, ensuring that customers receive the best products and support available in the market. As the industry continues to evolve, the company remains dedicated to meeting the ever-changing needs of its customers, solidifying its position as a leader in the global pumping industry.
Mud Tanks on Drilling Rig: Understanding their Importance and Functionality
Title: Mud Tanks on Drilling Rig: Enhancing Efficiency and Environmental ResponsibilityIntroduction:As the demand for oil and gas continues to rise worldwide, drilling companies are constantly seeking innovative solutions to improve efficiency, reduce costs, and minimize their environmental impact. One crucial aspect of the drilling process is the effective management of drilling fluids, or mud. In this article, we will delve into the significance of mud tanks on drilling rigs, exploring how they contribute to fluid management and the operational success of drilling companies. We will also examine the role of a leading drilling equipment provider in delivering advanced mud tank solutions that prioritize efficiency, safety, and environmental responsibility.Efficient Fluid Management:Mud tanks play a pivotal role in the drilling process, providing a centralized location for the storage, circulation, and treatment of drilling mud. These large tanks are integrated into drilling rigs and are carefully designed to meet the specific operational requirements of each drilling project. By efficiently managing the drilling fluid, mud tanks ensure the integrity of the wellbore, lubricate the drilling bit, and carry cuttings to the surface, thereby enhancing the drilling process's overall efficiency.Safety and Environmental Considerations:With increasing environmental consciousness, drilling companies are under pressure to minimize their environmental footprint. Mud tanks aid in this endeavor by effectively separating the drilling mud from the drill cuttings, allowing for proper treatment and disposal of these byproducts. This system ensures compliance with environmental regulations and facilitates responsible waste management.In addition, mud tanks are equipped with advanced safety features to protect workers and prevent accidents. These features include sensors, alarms, and containment measures that detect and mitigate any potential leaks or spills, preserving the wellbeing of the crew and surrounding environment.The Role of [Drilling Equipment Provider]:[Drilling Equipment Provider], a global leader in drilling solutions, has been at the forefront of developing state-of-the-art mud tank systems. Committed to engineering excellence, they continuously improve their products to meet the evolving needs of the industry. By deploying their cutting-edge mud tank technologies, drilling companies can optimize their operations while adhering to stringent safety and environmental standards.[Drilling Equipment Provider] employs a holistic approach, beginning with comprehensive research and development, and continuing through the manufacturing, installation, and ongoing support phases. Their mud tank systems are designed to deliver high-performance capabilities, ensuring efficient separation of liquid and solids, better fluid control, and enhanced drilling mud treatment.Moreover, [Drilling Equipment Provider]'s mud tank solutions incorporate innovative automation and monitoring features that allow for real-time data analysis. This enables drilling companies to optimize their fluid management, detect any potential issues promptly, and make data-driven decisions to ensure continuous operations.Conclusion:Mud tanks constitute a critical element in the drilling process, playing a significant role in enhancing efficiency, safety, and environmental responsibility. By partnering with industry leaders like [Drilling Equipment Provider], drilling companies can gain access to cutting-edge mud tank systems that optimize fluid management and reinforce their commitment to sustainable practices. With the continuous development of advanced technologies, the integration of highly efficient mud tank systems is ushering in a new era of drilling operations that are both productive and environmentally conscious.
Effective Mud Gas Separator Design for Oil and Gas Operations
Mud Gas Separator Design Innovations by Leading CompanyIn the oil and gas industry, the need to effectively separate gas from drilling fluid has led to the development of advanced technologies such as the Mud Gas Separator (MGS). One of the leading companies in this field, with a proven track record of innovation and excellence, is {}. Their latest MGS design is set to revolutionize the industry by offering improved performance and efficiency.Established in {}, {} has been at the forefront of developing cutting-edge solutions for the oil and gas sector. With a team of highly skilled engineers and researchers, the company has consistently delivered state-of-the-art equipment that meets the evolving needs of the industry. The company's commitment to quality, safety, and environmental protection has earned them a stellar reputation as a trusted partner for oil and gas companies around the world.The latest Mud Gas Separator design by {} is the result of years of research and development. This innovative technology is designed to effectively separate and vent gas from drilling fluid, ensuring the safety of personnel and equipment on drilling rigs. The new design incorporates advanced features that enhance performance and reliability, making it an invaluable tool for oil and gas operations.One of the key features of the new Mud Gas Separator design is its enhanced gas-liquid separation efficiency. Thanks to innovative engineering and advanced materials, the MGS is capable of effectively capturing and removing gas from drilling fluid, even in high-pressure and high-temperature environments. This not only improves safety on drilling rigs but also minimizes the risk of equipment damage and downtime.Furthermore, the new MGS design also incorporates a compact and lightweight construction, making it easier to transport and install on drilling rigs. This innovative approach to design and engineering reflects {}'s commitment to practicality and ease of use, ensuring that their products meet the needs of their clients in the field.In addition to its performance and portability, the new Mud Gas Separator design by {} also integrates advanced safety features. These include robust gas venting systems and fail-safe mechanisms, which are essential for ensuring the wellbeing of personnel and the protection of the environment during drilling operations.{}'s Mud Gas Separator design is also designed to be user-friendly, with intuitive controls and maintenance features that make it easier for operators to monitor and service the equipment. This focus on usability and accessibility is a testament to {}'s customer-centric approach, ensuring that their products are not only technologically advanced but also practical and easy to operate.With the launch of their latest Mud Gas Separator design, {} reinforces their position as a leading innovator in the oil and gas industry. This new technology is set to raise the bar for gas-liquid separation on drilling rigs, offering unparalleled performance, reliability, and safety. As the industry continues to evolve, {} remains dedicated to developing solutions that address the challenges of today and anticipate the needs of tomorrow. Their commitment to excellence and innovation is evident in every aspect of their business, making them a trusted partner for oil and gas companies worldwide.
Oilfield Centrifuge: The Latest Innovation in Oil Extraction Technology
Oilfield Centrifuge Revolutionizes Oil and Gas Industry OperationsThe oil and gas industry is one of the largest and most critical sectors in the global economy, responsible for meeting the world's energy needs. To keep up with the high demand for oil and gas, companies are constantly looking for new technologies and innovations to streamline their operations and increase efficiency. This is where the oilfield centrifuge, developed by {}, comes into play, revolutionizing the way oil and gas are processed and produced.The oilfield centrifuge is a crucial piece of equipment used in the oil and gas industry to separate solid particles from the drilling fluids, which are essential for the drilling and production of oil and gas. This process, known as dewatering and solids control, is crucial for maintaining the drilling fluids' properties and ensuring smooth and efficient operations. With the introduction of the oilfield centrifuge, this process has been completely transformed, providing companies with a reliable and cost-effective solution for their dewatering and solids control needs.The oilfield centrifuge developed by {} is designed with cutting-edge technology and engineered to provide high-performance and efficiency. This equipment is capable of separating a wide range of solid particles and contaminants from the drilling fluids, including fine particles that are difficult to remove using traditional methods. It can significantly reduce the volume of waste produced during the drilling process, leading to cost savings and environmental benefits.One of the key features of the oilfield centrifuge is its versatility and adaptability to various drilling conditions and fluid types. This equipment can handle high flow rates and large volumes of drilling fluids, making it suitable for both onshore and offshore drilling operations. With its robust construction and innovative design, the oilfield centrifuge is built to withstand the harsh conditions of the oilfield, ensuring reliable and consistent performance in any environment.In addition to its performance and efficiency, the oilfield centrifuge is also designed with user-friendliness in mind. It is equipped with advanced control systems and automation features that make it easy to operate and maintain. This allows companies to streamline their operations and reduce the need for manual intervention, ultimately saving time and resources.Furthermore, {} provides comprehensive support and services for the oilfield centrifuge, including installation, training, and maintenance. This ensures that companies are able to maximize the potential of this equipment and achieve the best results in their drilling and production operations. With its commitment to customer satisfaction and excellence, {} has established itself as a trusted partner for companies in the oil and gas industry.The introduction of the oilfield centrifuge has had a significant impact on the oil and gas industry, providing companies with a reliable and cost-effective solution for their dewatering and solids control needs. With its high-performance capabilities, versatility, and user-friendly design, this equipment has revolutionized the way drilling fluids are processed and produced, leading to improved efficiency and environmental sustainability.As the demand for oil and gas continues to rise, the oilfield centrifuge developed by {} is poised to play a key role in supporting the industry's growth and development. With its innovative technology and commitment to excellence, this equipment is set to be a game-changer for companies looking to optimize their operations and achieve success in the dynamic and challenging world of oil and gas.
Mud Pump for Drilling: The Latest Innovations in Chinese Equipment
Shanghai, China - China Mud Pump, a leading manufacturer of high-quality mud pumps for drilling applications, has announced that they are now offering a wide range of mud pumps for the drilling industry. With a strong focus on innovation and quality, the company has established a reputation for providing reliable and efficient equipment for oil and gas exploration, mining, and other drilling operations.The company is known for its commitment to continuous improvement and customer satisfaction. They have invested heavily in research and development to ensure that their products meet the highest standards of performance and reliability. In addition, they have a team of experienced engineers and technicians who are dedicated to providing comprehensive support and technical assistance to their clients.China Mud Pump's products are designed to meet the specific needs of the drilling industry, offering a variety of models with different specifications and features to accommodate various drilling conditions. These mud pumps are widely used in onshore and offshore drilling operations, providing the necessary pressure and flow rate to effectively remove drilling cuttings and maintain wellbore stability.In addition to their standard product line, China Mud Pump also offers customized solutions to meet the unique requirements of their clients. They work closely with their customers to understand their specific needs and provide tailored mud pump solutions that are efficient, reliable, and cost-effective.One of the key advantages of China Mud Pump's products is their focus on sustainability and environmental responsibility. They have implemented advanced technologies to minimize energy consumption and reduce environmental impact, ensuring that their equipment complies with the highest environmental standards.Furthermore, the company has a strong commitment to quality control and has implemented rigorous testing and inspection processes to ensure the reliability and performance of their mud pumps. This dedication to quality has earned them the trust and confidence of their customers, who rely on their products for their critical drilling operations.China Mud Pump's dedication to excellence extends beyond their products, as they also provide comprehensive after-sales support and service. Their team of skilled technicians is available to assist with installation, maintenance, and repairs, ensuring that their clients can rely on their equipment for the long term.With a strong focus on technological innovation, quality control, and customer satisfaction, China Mud Pump has positioned itself as a trusted partner for the drilling industry. As the demand for efficient and reliable mud pumps continues to grow, the company is well-equipped to meet the evolving needs of their clients and provide innovative solutions that enhance drilling productivity and efficiency.In conclusion, China Mud Pump is a leading manufacturer of mud pumps for drilling applications, offering a wide range of high-quality products designed to meet the specific needs of the drilling industry. With a strong commitment to innovation, quality, and customer satisfaction, the company is well-positioned to support the growing demand for efficient and reliable drilling equipment. Whether it's for onshore or offshore drilling operations, China Mud Pump's products and services have become the go-to choice for many drilling companies around the world.
Effective Dust Removal Equipment and Collector Systems in China
China's Dust Removal Equipment and Dust Collector industry is experiencing significant growth and innovation, as companies in this sector are working tirelessly to develop advanced and efficient solutions to combat air pollution and improve environmental quality. One company that is at the forefront of this endeavor is {}. With a strong commitment to research and development, the company has been able to produce state-of-the-art dust removal equipment and dust collectors that are setting new industry standards.Founded in {}, {} has quickly established itself as a leading manufacturer and supplier of dust removal equipment and dust collectors in China. The company's mission is to provide reliable and efficient solutions for controlling air pollution, and it has invested heavily in technology and talent to achieve this goal. Through continuous innovation and improvement, {} has developed a comprehensive range of products that cater to a wide variety of industrial and commercial applications.One of the key factors that sets {} apart from its competitors is its commitment to quality and performance. The company's dust removal equipment and dust collectors are built to the highest standards, using premium materials and cutting-edge technology. This not only ensures the durability and reliability of the products but also guarantees their effectiveness in removing dust and other airborne pollutants from the environment.In addition to its dedication to quality, {} also places a strong emphasis on environmental sustainability. The company understands the importance of reducing air pollution and its impact on public health and the environment. As a result, {} designs its dust removal equipment and dust collectors with energy efficiency and environmental responsibility in mind. By minimizing energy consumption and emissions, these products not only provide effective dust control but also contribute to a cleaner and healthier planet.Furthermore, {} is committed to providing superior customer service and support. The company works closely with its clients to understand their specific needs and requirements, and then offers customized solutions that meet and exceed expectations. With a team of experienced engineers and technicians, {} also provides comprehensive technical assistance, maintenance, and training to ensure that its customers can maximize the performance and longevity of their dust removal equipment and dust collectors.One of the most notable achievements of {} is its continued investment in research and development. The company allocates a significant portion of its resources to advancing the technology and capabilities of its products. This commitment has enabled {} to introduce cutting-edge innovations that have redefined the industry's standards for dust control. As a result, the company's dust removal equipment and dust collectors are known for their efficiency, reliability, and adaptability to various operating conditions.Looking ahead, {} is poised to further expand its influence in the global market. With a proven track record of success and a strong reputation for delivering high-quality solutions, the company is well-positioned to capitalize on the growing demand for advanced dust removal equipment and dust collectors. As air pollution continues to be a pressing concern worldwide, {} is prepared to play a leading role in promoting cleaner and safer environments through its innovative and sustainable products.In conclusion, {} is a trailblazer in the dust removal equipment and dust collector industry, and its contributions to environmental protection and air quality improvement are commendable. With its unwavering commitment to excellence, innovation, and sustainability, {} is set to make a significant impact on the global stage, and the future looks promising for the company and its mission to create a cleaner and healthier world.
Efficient and Reliable Mud Gun Helps Boost Productivity in [Specific Industry]
Mud Gun Revolutionizes Drilling Operations in the Oil and Gas IndustryIn recent years, the oil and gas industry has been undergoing significant technological advancements to enhance drilling operations efficiency and safety. Among the leading innovators in this field is a renowned company, which has developed a groundbreaking solution called the Mud Gun, revolutionizing the way drilling operations are conducted.Designed to address the challenges associated with drilling mud circulation, the Mud Gun is a state-of-the-art device that enables efficient and effective cleaning, preventing hazardous situations and optimizing drilling operations. With its cutting-edge technology and user-friendly interface, it has become an essential tool for drilling companies worldwide.The Mud Gun combines durability, practicality, and versatility, making it the preferred choice for drilling operations. Its unique design allows for easy installation on drilling rigs and its robust construction ensures long-lasting performance even in the harshest drilling environments.One of the key features of the Mud Gun is its efficient mud circulation system. By using high-pressure jets, it effectively cleans the drilling mud, removing solid particles and maintaining its consistency. This process helps prevent blockages in the drilling equipment, reducing downtime and ensuring smooth operations.Furthermore, the Mud Gun's intelligent control system allows operators to monitor and adjust mud pressure and flow rate, providing real-time data that aids in decision-making and enhances drilling efficiency. The user-friendly interface of the Mud Gun enables operators to have better control over drilling operations, ensuring maximum productivity and safety.With safety being a top priority in the oil and gas industry, the Mud Gun is equipped with advanced safety features. The device is fitted with multiple sensors and alarms that detect potential malfunctions, leaks, or abnormal conditions, promptly notifying the operators and preventing accidents.The Mud Gun's outstanding performance has made it an indispensable tool for drilling companies across the globe. By ensuring proper cleaning and maintenance of drilling mud, it contributes to the longevity of drilling equipment, lowering maintenance costs and increasing the profitability of drilling operations.In addition to its exceptional performance, the Mud Gun is committed to minimizing its environmental impact. It incorporates eco-friendly technologies that reduce mud waste and contamination, ensuring compliance with environmental regulations and promoting sustainable drilling practices.As the oil and gas industry continues to evolve, the role of technology in enhancing drilling operations cannot be overstated. The Mud Gun has emerged as a game-changer, providing drilling companies with a reliable, efficient, and environmentally-friendly solution that optimizes drilling processes.Through continuous research and development, the company behind the Mud Gun remains committed to innovation and staying at the forefront of the industry. Their dedication to excellence and customer satisfaction has earned them a stellar reputation as a leader in the field, trusted by drilling professionals around the world.With its cutting-edge technology and exceptional performance, the Mud Gun has truly revolutionized drilling operations in the oil and gas industry. By offering a reliable solution that enhances efficiency, safety, and sustainability, it has become an indispensable tool for drilling companies globally. As technology continues to advance, the Mud Gun is undoubtedly a testament to the endless possibilities of innovation in the field of drilling operations.
Compact Mixing Tank: A Game-Changer for Efficient Mixing Processes
Small Mixing Tank Company Works to Revolutionize IndustryFor years, companies in the chemical and pharmaceutical industries have relied on large mixing tanks to produce their products, but a small startup called Small Mixing Tank (SMT) is looking to change that.SMT has developed a compact, customizable mixing tank that is perfect for companies that need a more efficient and cost-effective solution. Their tanks come in a range of sizes and are designed to fit in tight spaces, making them ideal for smaller facilities or production lines. In addition, SMT’s tanks are equipped with sophisticated mixing technology that ensures a uniform blend of materials and reduces waste.“Large mixing tanks can be a real headache for companies that have limited space or need to move their production lines around,” said SMT founder and CEO, Jane Smith. “That’s why we decided to develop a smaller, more versatile option that can be customized to meet the needs of any industry.”One of the key features of SMT’s tanks is their modular design. Companies can choose from a range of mixing heads and blades to create a tank that is tailored to their specific needs. This eliminates the need for companies to purchase multiple tanks for different applications, saving them time and money in the long run.“Our tanks are really a one-stop-shop solution,” said Smith. “From pharmaceuticals to food and beverage, our customers can create a mixing tank that meets the demands of their industry without having to invest in multiple tanks and accessories.”SMT’s tanks are also designed with cleaning and maintenance in mind. The tanks are easy to disassemble and clean, reducing the risk of contamination or cross-contamination. Additionally, the tanks’ components are all easily replaceable, so companies don’t have to worry about costly repairs or downtime if parts need to be replaced.“We know that time is money in manufacturing, so we wanted to make sure our tanks were designed for easy maintenance and cleaning,” said Smith. “This minimizes downtime and ensures that our customers can keep their production lines running smoothly.”Since launching in 2020, SMT has seen impressive growth and has attracted the attention of several major companies. Recently, the company received a significant investment from a leading pharmaceutical firm, which will allow them to expand their production capabilities and offer even more advanced mixing technology.“We’re thrilled to have the support of such a well-respected company in the pharmaceutical industry,” said Smith. “This investment will allow us to take our mixing technology to the next level and further revolutionize the industry.”Looking to the future, SMT plans to continue enhancing its mixing technology and expanding its product line to meet the needs of different industries. The company also plans to explore new markets and opportunities for growth, with a focus on sustainability and reducing waste.“We believe that our tanks have the potential to transform the manufacturing industry and help businesses of all sizes operate more efficiently and sustainably,” said Smith. “We’re excited to continue pushing the boundaries and developing new solutions that benefit both our customers and the planet.” In conclusion, Small Mixing Tank has established itself in the industry as a company that is dedicated to creating innovative solutions for businesses of all sizes. With its compact, modular design and advanced mixing technology, the company’s tanks have the potential to revolutionize the industry and help companies operate more efficiently and sustainably. As SMT continues to grow and expand, it will be interesting to see how it continues to push the boundaries of what is possible in manufacturing.
High-quality Urethane Panel for Various Applications
[Company Name], a leading manufacturer of high-quality industrial products, has recently announced the launch of their new TH48-30X.85MT Urethane Panel. This new addition to their extensive product line is expected to meet the growing demand for durable and reliable urethane panels in various industrial applications.The TH48-30X.85MT Urethane Panel is designed to provide exceptional performance and longevity in challenging environments. Made from high-grade urethane materials, this panel offers superior resistance to wear, impact, and abrasion, making it ideal for use in mining, aggregate, and other demanding industries. Its unique composition also ensures excellent flexibility and elasticity, allowing it to withstand heavy loads and harsh operating conditions.With a dimension of 48 inches by 30 inches and a thickness of 0.85 inches, the TH48-30X.85MT Urethane Panel is suitable for a wide range of applications, including screen decks, chute liners, and other material handling equipment. Its versatile design and customizable options make it a cost-effective solution for businesses looking to enhance the performance and longevity of their equipment.In addition to its exceptional durability, this urethane panel is also designed for easy installation and maintenance. Its lightweight construction and flexibility allow for quick and hassle-free fitting, reducing downtime and labor costs. Furthermore, its non-corrosive and non-conductive properties make it a safe and reliable choice for various industrial settings.[Company Name] takes pride in its commitment to quality and innovation. With decades of experience in the industry, they have established a reputation for delivering high-performance products that exceed customer expectations. The introduction of the TH48-30X.85MT Urethane Panel further demonstrates their dedication to providing cutting-edge solutions that address the evolving needs of their clients."We are excited to unveil our latest urethane panel offering, the TH48-30X.85MT," said [Spokesperson Name], [Position] at [Company Name]. "This new product exemplifies our ongoing efforts to deliver superior quality and reliability to our customers. We believe that the TH48-30X.85MT Urethane Panel will provide a competitive advantage to businesses seeking durable and cost-effective solutions for their operations."In line with their commitment to sustainability, [Company Name] ensures that their urethane panels are manufactured using eco-friendly processes and materials. By prioritizing environmental responsibility, they aim to contribute to a cleaner and greener industry while delivering top-notch products to their customers.The introduction of the TH48-30X.85MT Urethane Panel underscores [Company Name]'s dedication to staying at the forefront of technological advancements and industry trends. As they continue to expand their product offerings, they remain focused on delivering unwavering quality, performance, and value to their diverse clientele.In conclusion, the launch of the TH48-30X.85MT Urethane Panel marks another significant milestone for [Company Name] as they continue to reinforce their position as a leader in the industrial products market. With its exceptional durability, versatility, and ease of use, this new offering is poised to set a new standard for urethane panels in the industry. As businesses seek reliable and long-lasting solutions for their operations, [Company Name] remains dedicated to providing innovative products that meet and exceed customer expectations.